Trip
New Member
Got a little of a dilemma what to do with this block of metal i have in the grage. (long post)
I had originally rebuild my engine with the main following parts:
Crank checked and balanced with JUN flywheel
ACL bearings
Rods checked and weight balanced
ARP rod bolts
ARP head bolts
JE pistons 86.5
HKS 1.2mm Gasket
Blocked checked, faced, bored and honed for pistons
Head de-assembled, checked and faced. Build it all with new parts, excluding cams and cam brackets. 3 angle valve job. Valves are original 54c size.
The engine turned out good and did the running-in without any problems. I changed the running-in oil/filter 3 times and finally to Silkolene Pro S 10w-50 ready to race.
After the first race which consists of 4 x 1minute runs, the engine started smoking drastically and coolant was almost finished from expansion tank. I first thought it was the turbo (GT2871R) since car was coming at full boost (10-12psi) at 5000rpm. Changed turbo but the symptoms remained.
With a lot of help and advise from Bob, I replaced the ARP head studs with the old OE I had without removing the head. This proved a success at first with no evident smoke from exhaust. But after leaving the car to cool down there was around an inch+ of coolant missing from the expansion tank. Filled it up again and repeated the test for 5 times. And every time coolant was missing. Strangely I didn’t find where the coolant was going. I had no coolant underneath the engine neither did I have steam/mist coming up. There was no evident of white smoke coming from exhaust either but i could have had just a faint mist I couldn’t see with my eyes. Oil was clean with no traces of coolant or mayo. Bubbles were coming out from the radiator though.
I decided to remove head and check the gasket. Cylinder 1 was dry, No2 was a little wet, No3 had oil, and No4 was like No2. Gasket was not in a good state either. See pics below
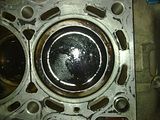
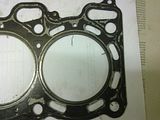
Replaced the gasket with a Cosworth 1.2mm and used the same old OE bolts. Bolted everything in place and retested. Yet again, Identical same results. I performed a compression test and it showed 160psi, 161psi, 165psi, 160psi. (pics below) Time was running out. I simple dropped the whole engine with gearbox and replaced it with a standard lump until the race season is over.

Race season is over and decided to give it another try. I took the head to the engineer to test it out. It came back with a straight face and he even told me it didn’t leak (whatever that means).
I will take the block next but I really doubt its warped or anything of the sort.
I am thinking that the first time the ARP head studs were to blame and the second and third time the OE old bolts were stretched enough not to fully torque the head down.
Any suggestions what else could it be ? I was hoping to start the season with at least 1 bar of boost
I had originally rebuild my engine with the main following parts:
Crank checked and balanced with JUN flywheel
ACL bearings
Rods checked and weight balanced
ARP rod bolts
ARP head bolts
JE pistons 86.5
HKS 1.2mm Gasket
Blocked checked, faced, bored and honed for pistons
Head de-assembled, checked and faced. Build it all with new parts, excluding cams and cam brackets. 3 angle valve job. Valves are original 54c size.
The engine turned out good and did the running-in without any problems. I changed the running-in oil/filter 3 times and finally to Silkolene Pro S 10w-50 ready to race.
After the first race which consists of 4 x 1minute runs, the engine started smoking drastically and coolant was almost finished from expansion tank. I first thought it was the turbo (GT2871R) since car was coming at full boost (10-12psi) at 5000rpm. Changed turbo but the symptoms remained.
With a lot of help and advise from Bob, I replaced the ARP head studs with the old OE I had without removing the head. This proved a success at first with no evident smoke from exhaust. But after leaving the car to cool down there was around an inch+ of coolant missing from the expansion tank. Filled it up again and repeated the test for 5 times. And every time coolant was missing. Strangely I didn’t find where the coolant was going. I had no coolant underneath the engine neither did I have steam/mist coming up. There was no evident of white smoke coming from exhaust either but i could have had just a faint mist I couldn’t see with my eyes. Oil was clean with no traces of coolant or mayo. Bubbles were coming out from the radiator though.
I decided to remove head and check the gasket. Cylinder 1 was dry, No2 was a little wet, No3 had oil, and No4 was like No2. Gasket was not in a good state either. See pics below
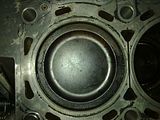
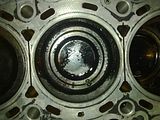
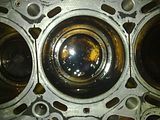
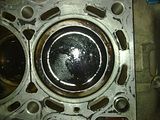
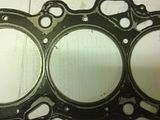
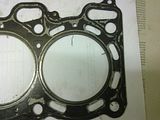
Replaced the gasket with a Cosworth 1.2mm and used the same old OE bolts. Bolted everything in place and retested. Yet again, Identical same results. I performed a compression test and it showed 160psi, 161psi, 165psi, 160psi. (pics below) Time was running out. I simple dropped the whole engine with gearbox and replaced it with a standard lump until the race season is over.




Race season is over and decided to give it another try. I took the head to the engineer to test it out. It came back with a straight face and he even told me it didn’t leak (whatever that means).
I will take the block next but I really doubt its warped or anything of the sort.
I am thinking that the first time the ARP head studs were to blame and the second and third time the OE old bolts were stretched enough not to fully torque the head down.
Any suggestions what else could it be ? I was hoping to start the season with at least 1 bar of boost